All GRP is not the same
Automotive engineering in particular has long relied on glass fibre-reinforced plastic. Mechanical engineering and other industries are also recognising increasing potential, as the material has many advantages over conventional materials. Strength and formability are at the forefront of its capabilities. GRP also scores highly with its excellent weight/strength ratio. This is particularly important when the material is used for the production of components.
The differences in GRP begin before the manufacturing process, during the composition of the material and extend to the finished product. We have summarized for you how the composition of GRP can differ. We will also show you the forms that GRP can take and the differences that exist in the manufacturing process.
Composition determines the characteristic features
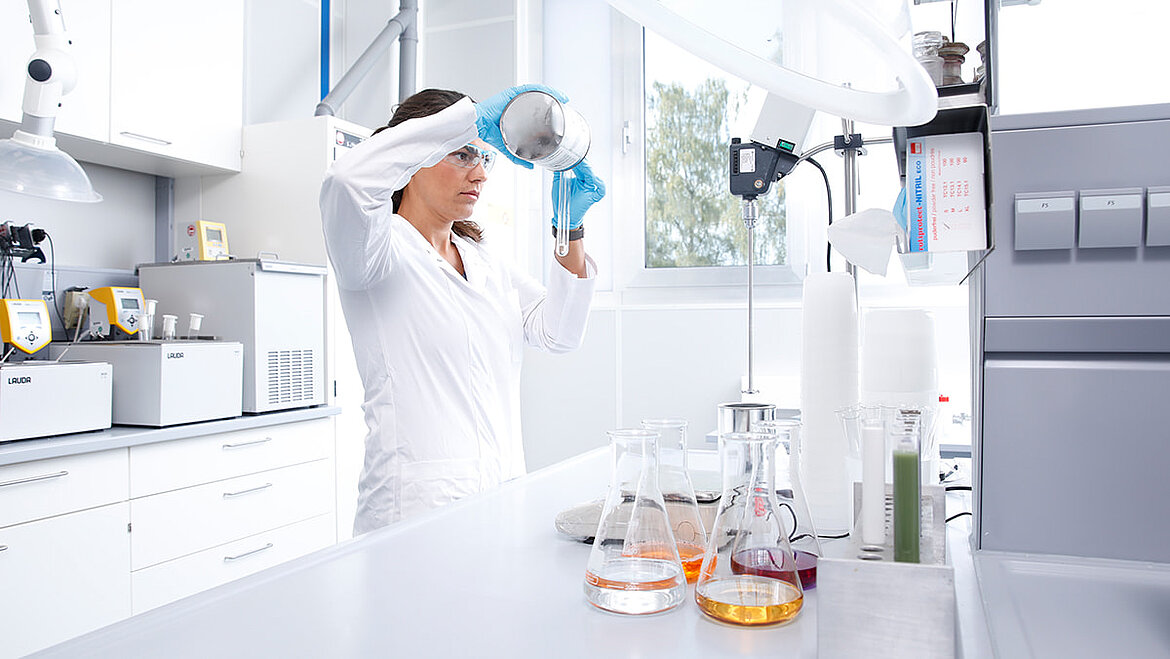
GRP stands out among materials in particular as it is light but extremely robust. This is due to the special composite of glass fibres and a plastic matrix. The matrix gives the fibre composite material its appearance, while there are few limits to the colour and the surface structure. From a mechanical perspective, the matrix must hold the reinforcing fibres in place and transfer and distribute stresses between them. In terms of durability, it has the task of protecting the fibres from external mechanical and chemical influences. The size of the glass fibres is also important here. This must be compatible with the matrix resin to ensure that the fibres and the matrix bind.
In the composition of the raw materials of GRP, unsaturated polyester resin or epoxy resin is usually used as a matrix. The easiest way to choose between polyester resin or epoxy resin is to compare the advantages and disadvantages of polyester resin and epoxy resin.
Unsaturated Polyester Resins (UP)
Polyester resin is easily processed with glass fibre mats. The main reasons why glass fibre textiles and polyester resin are so compatible are the excellent impregnation and fibre bonding. In addition, polyester resin is cheaper than epoxy resin and is easier to handle and generally easier to process. Unsaturated means that long, non-cross-linked polyester chains are still responsive because they have unused double bonds. If these are then reacted with the also unsaturated styrene, for example, this causes a cross-linking of the chains. This cross-linking reaction is called curing. The hardener quantities depend on the process and are determined by the manufacturer in complex tests. Depending on the choice of primary materials and mixing ratios, variable degrees of cross-linking are possible with UP resin, i.e. end products with varying hardness.
However, caution must be taken: The cross-linking reaction is highly dependent on the formulation and process and errors can lead to insufficient material characteristics. In addition, an odour characteristic of UP resins forms during curing. This is due to the fact that the styrene contained in the polyester resin evaporates to some extent during curing and, on the other hand, a small proportion of residual styrene remains in the final product. The odour threshold of styrene is in the ppm range. Polyester resin combined with reinforced fibres also has less pronounced mechanical properties than epoxy resin.
Epoxy Resins (EP)
Epoxy resins can score points by having more pronounced mechanical properties when combined with reinforcement fibres. This is mainly due to the fact that epoxy resin has excellent adhesive properties, which are also illustrated by strong fibre adhesion. In addition, epoxy resin shrinks less during curing than polyester resin, which is particularly advantageous in tool and mould making. Epoxy resin is also very popular for indoor use, as it is generally odourless. Epoxy resin does a good job not only in dry conditions, but also in water. Epoxy resin is highly resistant to hydrolysis. This also helps the EP resin to retain its structure in the water. That's why epoxy resin is also perfect for GRP parts exposed to water.
However, even epoxy resin is not perfect and has some disadvantages. The exact epoxy resin/epoxy hardener ratio must be maintained when mixing. Addition of excessive hardener leads to brittleness of the component, while insufficient hardener hinders full curing. In addition, epoxy resin can only be processed to a limited extent with glass fibre mats. This is because the binder in glass fibre mats weakens the matrix and if the binder concentration is high, the mechanics will suffer. It is therefore recommended that epoxy resin is processed with glass filament woven roving, glass fibre non crimp fabrics or carbon woven roving.
Differences in the glass fibre composite
It is not only the matrix that plays an important role in the composition, the choice of fibres is also decisive for the final product and its properties. The fibres give the fibre composite the necessary strength. In addition to tensile strength, bending strength can also play a role if the material is subjected to pressure. Since the fibres can be aligned according to the load and their density, i.e. the number per area, can be adjusted, tailor-made components are created with the help of appropriate production processes. There are various textile forms that are distinguished in the glass fibre composite: nonwovens, mats, woven roving and non-crimp fabrics.
Mats
Mats are made of cut glass fibres approx. 5 cm long or endless glass threads, which are continuously layered and bonded by a binder. If the glass fibres have already been formed as coils before the GRP production process, they are referred to as mats.
- various grammages (area weight): 200-500 g/m2
- randomly layered glass fibres, bonded with binder:
- "Chopped glass mat" or "chop mat" standard
- "infinite" fibres: better mechanical properties, but much more expensive
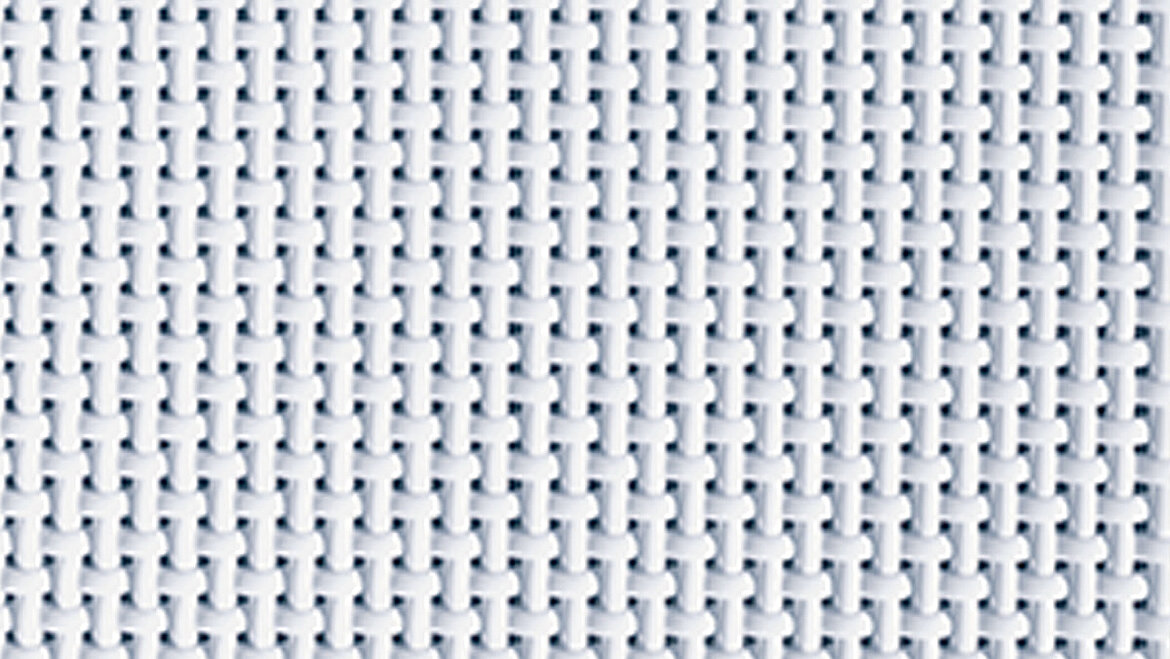
Woven Roving
Glass fibre rovings or yarns that are combined with fabric with different woven patterns are referred to as woven roving. In the case of woven roving, the strands are not bonded together. A roving is a bundle of fibres that are not connected to one another, but just lie next to one another.
- different grammages (area weight): 200-1000 g/m2
- Available as yarn or roving fabric
Non-crimp fabrics
In a non-crimp fabric, the glass fibre strands lie parallel and stretched into one or more positions. The positions are fixed at cross-over points by additional threads, usually made of polyester.
- different grammages (area weight): 100-1000 g/m2
- multi-directional arrangement, i.e. fibres in longitudinal and transverse direction and also in both diagonal directions (0°, 90°, 45°)
Different forms require different manufacturing processes
GRP is available in a wide range of applications from the automotive industry to the construction industry. Whether the smallest cables or entire aircraft parts - GRP can take on very different forms. Basically, glass-fibre reinforced plastics can be divided into three groups in which they are produced ready-made or for further processing: Moulded parts, sheets or rolls. Depending on the shape and use of the component, a distinction can be made between different manufacturing processes that specialize in producing GRP either as an individual moulded part, sheet or roll. Four different manufacturing processes are differentiated.
Sheet Moulding Compound (SMC)
Sheet moulding compound, also known as SMC, refers to typical press compounds made of thermosetting resins and glass fibres for the production of fibre-reinforced compounds. The SMC mass contains the necessary components that are fully premixed for processing. Polyester or vinyl ester resins are generally used. The reinforcement fibres are available in mat or woven roving form.
Applications for SMC
SMC is used to manufacture body parts for passenger vehicles, sports equipment, the electrical industry, the sanitary industry and the aerospace industry. Fasteners can already be inserted into the press mould during pressing. This makes SMC particularly economical. The fillers are used to reduce weight and costs.
Bulk Moulding Compound (BMC)
Bulk Moulding Compound, BMC for short, is a fibre-matrix semi-finished product consisting of short and long fibres. More precisely, it mostly consists of short glass fibres and a polyester resin. BMC is available as a dough-like, shapeless mass and is supplied in bags or other containers. Processing takes place in the hot-press process. The BMC mass is placed centrally in a heated, split tool. By closing the tool, the BMC is distributed and forms the desired product. Due to the short fibre lengths, thin ribs and wall thicknesses can also be filled during pressing. With correspondingly short fibre lengths, BMC can also be processed in the injection moulding process.
Applications for BMC
BMC is primarily used in the electrical sector. It is processed into switch components for low- and medium-voltage devices, where the specifications for switching performance and flame resistance are high. In the automotive sector, BMC is mainly used for headlight reflectors and carburettor housings.
Continuous Production Process
The continuous production process is a production process that ensures particularly high quality. LAMILUX Composites specializes in this process. GRP coils are manufactured on flat conveyor systems that are more than a hundred metres long. Due to the high degree of automation, which ensures that the different material variants can be reproduced at any time, the systems are the most modern of their kind in Europe. Throughout the entire production process, the production standards are safeguarded by seamless quality management. In addition to monitoring the process, this also includes intensive laboratory checks of incoming raw materials and final materials.
Manual Lamination
Manual lamination is one way of manufacturing complex components from fibre-reinforced plastic. Sizes vary up to that of gliders and recreational boats. This manufacturing process requires a negative form of the component to be manufactured, the required fibre fabric, for example glass fibre mats, and the matrix, for example epoxy resin. The two materials are then alternately distributed manually in the mould. During production, it is essential to ensure that the two components are well mixed, that the fibres are saturated with the matrix and that there are no air pockets. Afterwards, the component must either harden cold in the air or hot in a hardening oven. Hot hardening creates higher strengths and accelerates the curing process.
You can read even more information about glass fibre reinforced plastics, how the material compares with other materials and in which areas GRP is used, in our free white paper: